
NEWS
Advantages and disadvantages of the use of wear-resistant castings produced by lost foam casting pro
Views: Release date:2016-08-23
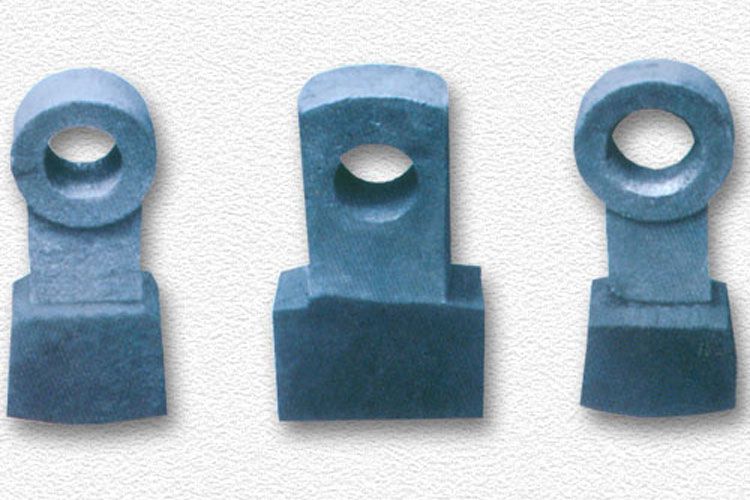
In recent years, the advantages of using the EPC process for producing wear-resistant castings which from the specific circumstances of each manufacturers is following:
- Good casting surface quality, high precision casting size, less defects and smooth surface, which will help improve the wear resistance of casting;
- We can produce high manganese steel and alloy steel material series which from wear-resistant materials and small thin-walled high manganese steel castings, it can save manpower and energy when water quenched immediately after casting solidification;
- sand can be reused up to 96% when we use dry quartz sand and Baozhu sand, it can solve the chronic problem of waste sand, it makes environmentally friendly and low-carbon economy;
- For the mill diaphragm plate, grid plate and crusher grate plate, the castings become high precision size and more favorable when using EPC technology.
- For the small factory who has venues with a small EPC production process, it is more appropriate due to small space and less investment, fast effects and so on.
- slag discharge difficultly when heavy castings of lost foam
- carburizing easy to occured when low-carbon steel castings, it causes trouble in melting and heat treatment, and some manufacturers has solved some solution by pouring to adopt after the first firing process;
- EPC manufacturers should provide not only equipment, but also the casting process.
- Lost foam casting Riser should have design specification, it should promote the use of CAE analysis system for casting molding and solidification simulation to determine a reasonable gating system.
Previous:Without
Next:Casting V production of wear-resistant castings has six advantages