
NEWS
THE SMART GUIDE TO MANGANESE AND HIGH CHROME CASTINGS
Views: Release date:2016-11-26
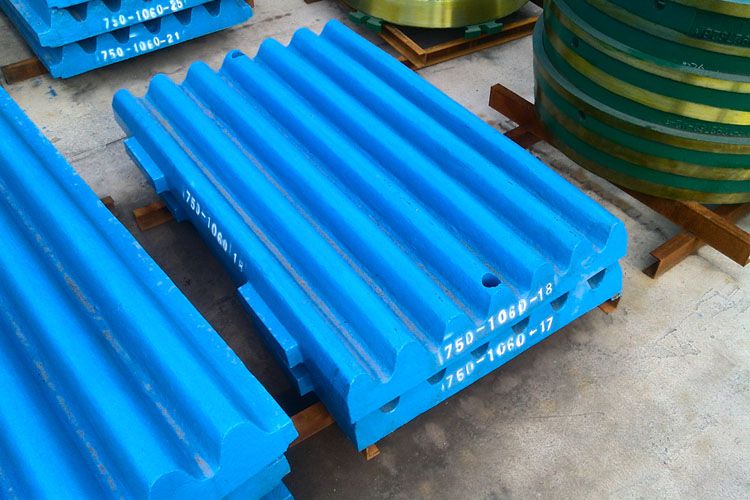
Practically every crushing operation these days is looking for ways to cut costs and increase production. One way you can find a lot of potential savings is by carefully choosing the right manganese castings. Look closely at your entire crushing operation from start to finish: the material you’re crushing, the type of crusher you’re using. Give extra attention to the profile of the crushing parts. By matching the profile of the manganese part to your operation’s requirements, you can run more efficiently with less downtime and lower operating and maintenance costs.
Here’s a list of factors to consider before you buy manganese castings. Asking the right questions before buying can save you money now and lower-costs of future operations. Manganese content is critical to the wear life of your crusher parts and the cost efficiency of your operation.
Manganese content can range between 9% - 24% and is usually referenced as;
14% = 13-14% MN
18% = 17% - 19% MN
21% = 21% - 24% MN
Castings with any of these manganese percentages could be the right ones for your application. It just depends on what you’re crushing. While you could use a higher percentage of manganese for cones or jaws, 14% manganese can work fine for hard non-abrasive materials especially with Wear and spare parts heavy duty Jaws. Remember manganese must “work-harden” for optimum performance, which should be matched with material hardness. The hardness & abrasiveness of the rock to be crushed should determine the manganese content for your operation.