
NEWS
High Manganese Liner Casting Process
Views: Release date:2017-05-22
High manganese liner widely used in quarrying,crushing and some other area.However, its need change very frequently if the quality not good. Casting process play an important role in controlling high manganese liner.
High Manganess Casting Material Chemical Composition(%)
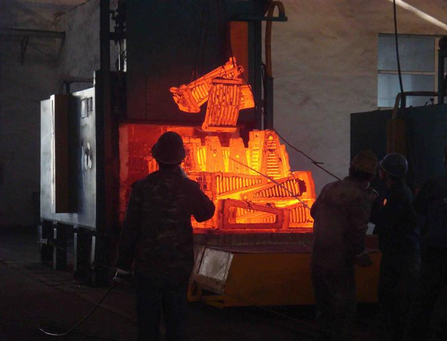
Many plants, welding and welding become inevitable. Selection of austenite-based manganese-nickel electrode (D256 or D266 type), specifications slender, φ3.2mm × 350mm, the outer coating is alkaline. Operation with a small current, weak arc, small welds multi-layer, always keep the low temperature and less heat operation method. While welding side of the hit, to eliminate stress. Important castings must be tested.
Hubei JYS Advanced Wear Resistant Material Technology Co.;Ltd specialized in manufacturing high manganese liner over 30 years. Our manganese liner include: jaw plate, cone liner, bowl liner,liner plate. If you need high manganese liner,please let me know!
Chemical Composition
In China,there are 3 types grades which based on the different content of carbon content,it range from 0.75% to 1.45%. The 3 types manganese materials are: Mn14Cr2,Mn18Cr2 and Mn22Cr2.High Manganess Casting Material Chemical Composition(%)
Material Code | C | Mn | Si | Cr | P | S |
Mn14Cr2 | C:0.9-1.3 | Mn:11.0-14.0 | Si:0.3-1.0 | Cr:1.5-2.5 | P:≤0.06 | S:≤0.04 |
Mn18Cr2 | C:1.1-1.5 | Mn:16.5-19.0 | Si:≤0.8 | Cr:1.5-2.5 | P:≤0.07 | S:≤0.04 |
Mn22Cr2 | C:1.1-1.4 | Mn:20-24 | Si:≤0.8 | Cr:1.5-2.5 | P:≤0.07 | S:≤0.04 |
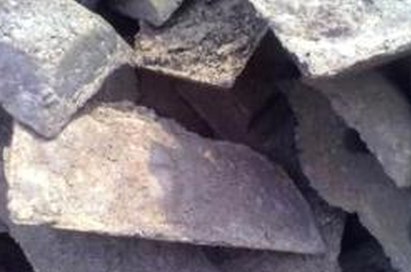
Smelting Process
First of all,we need focus on the order of addition, whether with the IF furnace, or electric arc furnace smelting, always smelting carbon steel, and all kinds of ferromanganese and other precious alloy materials, should be divided into several times, each time a small amount of furnace, precious elements should add in the last so as to reduce burns. Block should be as small as possible to 50-80mm is appropriate. After melting, the furnace temperature reaches 1580-1600 ℃, to deoxidation, dehydrogenation, denitrification, available aluminum wire, can also be Si-Ca alloy or SiC and other materials. The deoxidizer will be pressed into the depths of the furnace. Metal surface at this time with a cover agent cover, cut off the outside air. But also calm for some time, so that oxides, inclusions have plenty of time to float. However, many companies, only aluminum wire and even aluminum, sprinkle metal surface, and not covered, would not waste it! During this period, timely use of carbon ferromanganese to adjust the manganese and carbon content.Casting Process Design
Manganese steel is characterized by condensation shrinkage, poor heat dissipation, therefore, in the process design casting shrinkage rate of 2.5% -2.7%, casting the longer, the more should take the upper limit. Sand and sand core of the concession must be better. The gating system is open. A plurality of dispersed runners are introduced from the thin wall of the casting and are flat and wide, and the cross-sectional area near the casting is greater than the cross-sectional area associated with the runner, allowing the molten metal to be injected into the mold quickly and smoothly , To prevent the entire mold temperature difference is too large. Riser diameter is greater than the diameter of the hot section, close to the hot section, the height is 2.5-3.0 times the diameter, must be used hot riser even pour riser together, so that sufficient high temperature metal liquid to cast in the solidification shrinkage when the vacancy The It is also correct to place the sprue and the riser at the height. Pour as little as possible when pouring low temperature. Once the solidification, to timely loose box. Smart designers are always good at using cold iron, including the cold iron out of the cold iron, which not only refine a crystallization, to eliminate shrinkage, shrinkage, but also improve the production rate, of course, the appropriate dosage and specifications should be considered of. The cold iron to be clean, easy to melt, the amount of less appropriate. The three-dimensional size of the cold-rolled iron is a function of 0.6-0.7 times the three-dimensional dimension of the coolant. Too small does not work, too large cause casting cracking. Casting in the type of long-term insulation, until below 200 ℃ and then open the box.Heat Treatment
Heat treatment cracking, is caused by too fast temperature rise. So the correct operation is below 350 ℃, heating rate <80 ℃ / h, 750 ℃ below, <100 ℃ / h, and there are different periods of insulation. To> 750 ℃, the casting was plastic state, you can quickly heat up. To 1050 ℃ according to the thickness of the casting to determine the holding time, and then rose to 1100 ℃ or more. Give the furnace cooling room and then enter the water as soon as possible. High temperature heating is too slow, holding time is too short, after the bake to the water time interval is too long (not> 0.5min), all this affects the quality of castings. Into the water temperature should be <30 ℃, quenching, water temperature <50 ℃, water should not be less than 8 times the weight of casting. The cold water enters from the bottom of the tank and the warm water flows out of the top surface of the tank. Casting in the pool to three directions kept moving.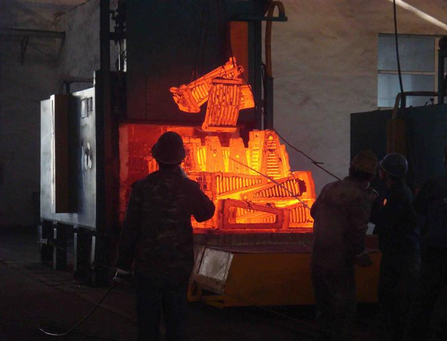
Cutting And Welding
Because manganese steel thermal conductivity is poor, so the cutting riser should pay great attention. It is best to cast the cast in the water, the cutting part of the exposed water, cutting a certain amount of stubble, heat treatment after grinding off.Many plants, welding and welding become inevitable. Selection of austenite-based manganese-nickel electrode (D256 or D266 type), specifications slender, φ3.2mm × 350mm, the outer coating is alkaline. Operation with a small current, weak arc, small welds multi-layer, always keep the low temperature and less heat operation method. While welding side of the hit, to eliminate stress. Important castings must be tested.
Hubei JYS Advanced Wear Resistant Material Technology Co.;Ltd specialized in manufacturing high manganese liner over 30 years. Our manganese liner include: jaw plate, cone liner, bowl liner,liner plate. If you need high manganese liner,please let me know!