
NEWS
we provide the very highest quality crusher wear parts
Views: Release date:2016-11-26
At Wear and Spare Parts, we provide the very highest quality wear parts available to the crushing and screening markets globally.
As a customer you can have full confidence in all our products as our foundry partners have extensive quality control procedures which are supported by our own quality assurance team. Our complete range of parts are regularly tested to ensure that they meet our customer's high expectations. These robust measures ensure all parts are of the highest standard, guaranteeing you exceptional wear life and value for money.
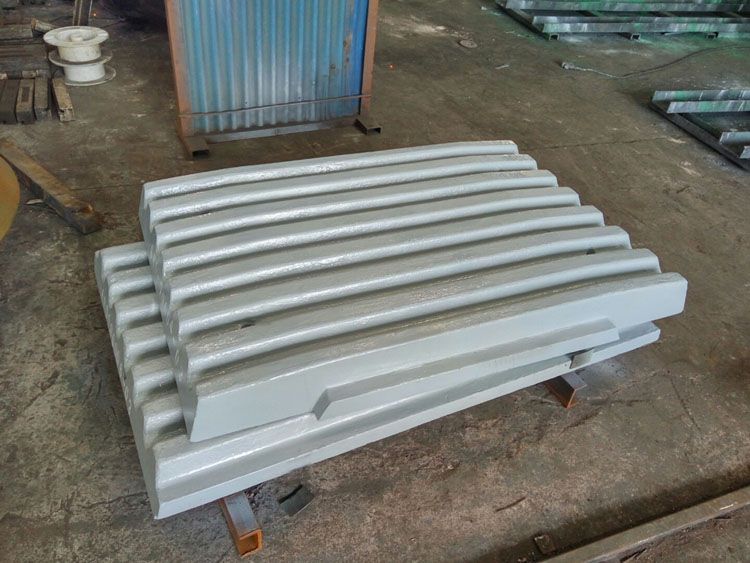
JAW CRUSHER WEAR PARTS
Critical factors for jaw crusher wear parts are how long they last and how efficiently they crush the material. Jaw weight, tooth profile and proper fit are all important considerations for efficient crushing. Efficiency requires proper tooth design. Tooth profile can be determined for each crushing application with the help of our experienced service representatives.
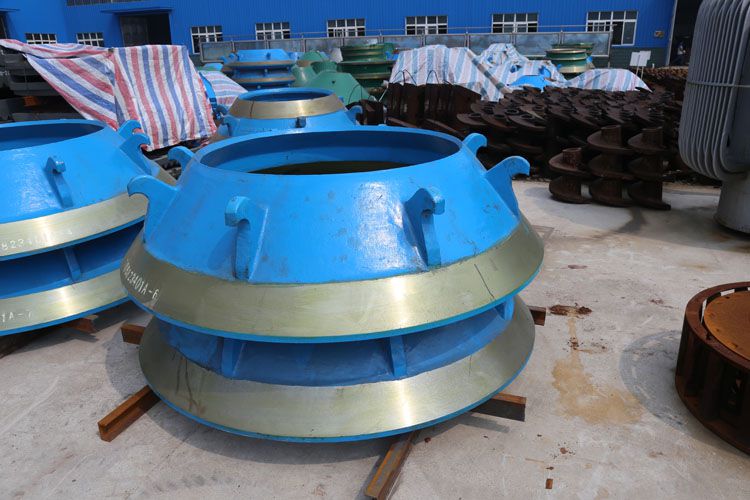
CONE CRUSHER WEAR PARTS
The critical factors for cone crusher parts are the open and closed side feed settings. The reduction ratio is the top size of the feed opening divided by the closed side setting (CSS) in inches. Reduction ratio will help determine the proper profile for each operation — most options are coarse, medium, and fine profiles. Be sure to match the profile to your crushing needs. Also check the product wear of mantle and bowl liners to confirm wear patterns.
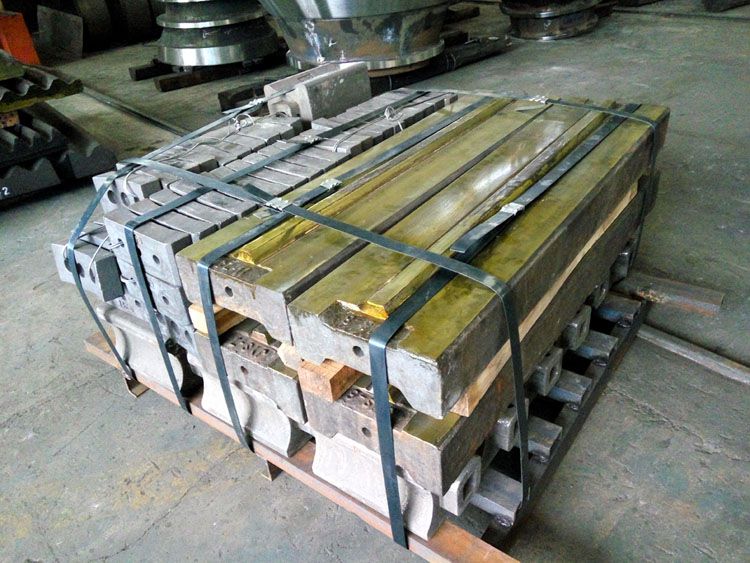
HSI CRUSHERS
Horizontal shaft impactor (HSI) crushers are both characterized by low capital costs and properly scheduled maintenance. It’s important to minimize these costs and maximize plant uptime by selecting the correct alloy for wear parts. Impact crushers are application-sensitive so you need to consider feed size, type of material and the desired product. HSI crushers, for example, are commonly used by quarry operations, sand and gravel producers and recyclers (where there might be metal in the material.) Selecting the wrong alloy can cause breakage of bars, accelerated wear and catastrophic failure to the crusher.